Streamline and optimize design for composite materials
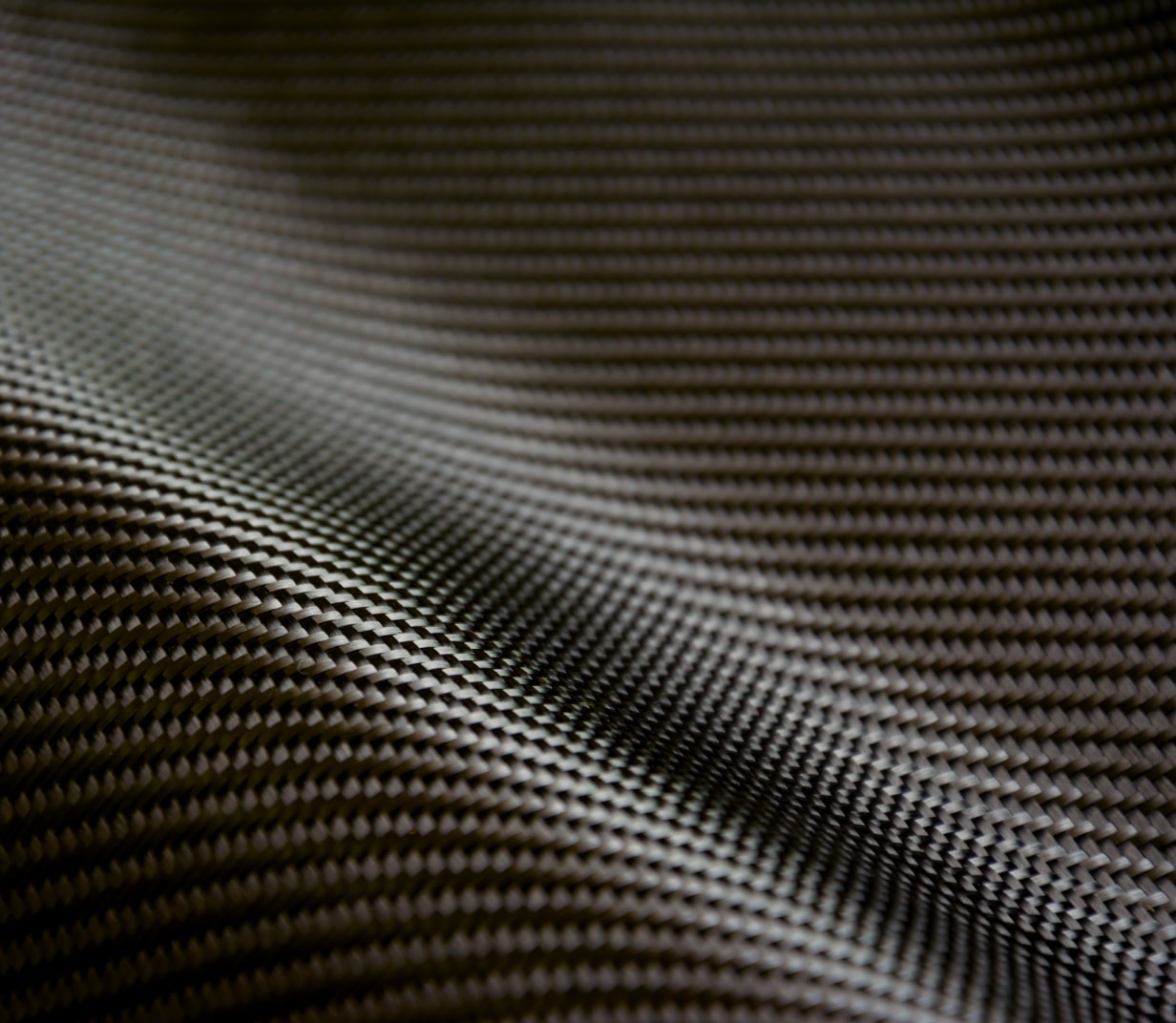
Fibersim maximizes the performance potential of your composite materials
Improve composite part performance and efficiency
-
01
Integrate design
Fibersim is embedded within leading CAD systems, allowing engineers to create designs for composite parts directly within their familiar CAD environment. Define the orientation, material type and thickness of composite layers directly on the CAD model.
- 02 Simulate the manufacturing processes
- 03 Optimize manufacturing processes
- 04 Create documentation and ply books
- 05 Ensure quality
- 06 Collaborate and manage data
Optimize composite material simulation
Support the product lifecycle of composite material
Utilize easy-to-use design simulation tools
Predict manufacturing issues
Manage materials effectively
Access accurate information
Improve productivity and reduce errors
Client success is our success
Applied CAx has been instrumental in providing advice and guidance when making critical decisions and implementing the correct solution to support our business processes. In an emerging industry such as Fusion, we face unique challenges every day. Applied has helped us pave the way in the digital transformation journey for this industry.
CFD has been the backbone of PacMar Technologies’ engineering advantage in the marine industry, and it’s really helped us accelerate our design process to get to working prototypes. PacMar is pushing the limits of the CFD code, and Applied CAx support helps facilitate it.
I greatly appreciate Applied CAx’s focus on providing practical solutions to real-world engineering problems, customer support and world-class training courses. They are a true partner in helping us expand our digital capabilities.
I highly recommend Applied CAx as a trusted partner for any organization seeking innovative software solutions. Their expertise, commitment to excellence and ability to meet the unique requirements of the aerospace industry have been instrumental in our success at Rocket Lab.
Most larger firms struggle to understand our unique desires. Not Applied CAx. It’s as if they intuitively grasp why we’re not like the competition—and why that matters. This collaboration, along with a bent for action, is the underpinning of our Engineering Digital Transformation.
AppliedCAx has been fantastic in helping us scale our growing business with the necessary software tools appropriately and cost effectively. Additionally, and on multiple occasions, Applied has been invaluable to us by providing immediate, quick turn-around licensing requests that proved vital in being able to serve our customers.
Applied CAX has been the definition of a strategic partner to X-Energy.
They have demonstrated their expertise in both the technology as well as the unique challenges in the Nuclear Industry daily. Our company faces immense challenges in adopting innovative digital engineering capabilities, and the thought leadership and executive engagement from Applied CAx has made all of the difference and accelerated our adoption of these cutting-edge tools and processes.
The future success of X-Energy with respect to Design, Analysis, Build, and Operations has been positively impacted and strengthened by our partnership with Applied CAx and their team.